Вопрос надежности оборудования стоит особенно остро на предприятиях с непрерывным производственным циклом. Малейший сбой может привести к значительным финансовым потерям, простоям и даже репутационным рискам. Один из ярких примеров того, как неправильный выбор комплектующих привел к критическим последствиям, произошел в марте 2025 года на продуктовом комбинате.
1. Дешево и быстро: чем обернулась экономия на запчастях
В феврале 2025 года на газопоршневой электростанции завода выявили трещину в горячей части корпуса турбины. Руководство решило заменить два турбонагнетателя. Столкнувшись со сложностями в логистике и долгими сроками поставки у проверенных производителей, заказчик выбрал более доступные неоригинальные запчасти из Юго-Восточной Азии.
Детали прибыли в марте 2025 года — месяц ожидания казался разумным компромиссом между ценой и характеристиками. Однако последствия оказались столь «непредсказуемыми», что их предвидели все, кроме тех, кто принял решение о покупке.
2. Процесс замены: всё по регламенту, но с неверным исходом
Монтажные работы выполнялись строго по стандартам регламентных работ.
Первые тестовые показатели после запуска соответствовали нормативам, что дало ложное ощущение успешности замены. Однако уже через 1 час 7 минут работы произошла авария.
3. Аварийная ситуация на ГПУ и её последствия
Через 1 час 7 минут после запуска системы произошло разрушение обоих турбонагнетателей. Это вызвало цепную реакцию с рядом серьёзных последствий
🔸 Полное разрушение роторов турбин. Лопасти турбонагнетателей разлетелись на осколки, что привело к деструктивным процессам внутри системы.
🔸 Повреждение интеркулера металлическими обломками. Осколки разрушенных турбин попали в интеркулер, что вызвало его разгерметизацию и полную неисправность.
🔸 Загрязнение маслом выхлопного тракта. Около 20 литров масла вытекло в систему выхлопа, что потребовало дорогостоящей очистки и утилизации загрязненных элементов.
🔸 Снижение давления в системе. Моментальное падение давления привело к сбоям в работе вторчиных узлов газопоршневой электростанции
🔸 Вынужденный простой производства. Производственная линия была остановлена на несколько дней, что привело к невыполнению заказов, потерям клиентов и репутационным издержкам.
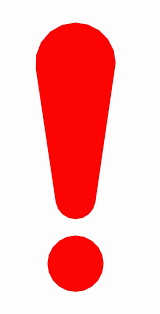
Эта авария нанесла серьёзный удар по всей производственной цепочке, вызвав не только финансовые убытки, но и организационные трудности. Восстановление полноценной работы электростанции потребовало закупки новых турбонагнетателей, дополнительного ремонта сопутствующих узлов и многодневной работы технического персонала.
4. Техническая экспертиза: что пошло не так?
Проведённый анализ разрушенных деталей выявил целый ряд критических дефектов, которые в совокупности привели к фатальному исходу. В первую очередь, было выявлено несоответствие материалов – использованные в турбокомпрессоре сплавы не обладали достаточной жаропрочностью, что привело к их быстрому перегреву и деформации. Под воздействием высоких температур металл терял свои механические свойства, становился хрупким и растрескивался, что в конечном итоге и вызвало разрушение корпуса турбонагнетателей.
Кроме того, выявлены серьёзные проблемы с балансировкой роторов. Их центровка оказалась выполнена с недопустимыми отклонениями, что привело к возникновению избыточных вибраций. Постоянные динамические нагрузки резко усилили износ подшипников и опорных элементов. Вибрация также негативно повлияла на соединительные узлы, вызвав ослабление крепежа и разгерметизацию масляной системы.
Дополнительные исследования выявили грубые нарушения технологии термообработки металла. В критически нагруженных местах структура материала оказалась неравномерной – отдельные участки имели повышенную хрупкость, что способствовало быстрому разрушению под действием механических и тепловых нагрузок. Дефекты литья и механической обработки дополнили этот ряд – в роторных элементах обнаружены микротрещины, которые, вероятно, присутствовали с момента производства.
Всё это в комплексе стало причиной аварии. Решение в пользу более дешёвых альтернатив обернулось критическими последствиями.
5. Как избежать подобных ошибок? Рекомендации по выбору запчастей для газопоршневых установок
Чтобы минимизировать риски, связанные с выбором запчастей, стоит придерживаться следующих принципов:
- Приоритет оригинальных запчастей. Оригинальные комплектующие соответствуют заводским требованиям и проходят строгий контроль качества.
- Проверка сертификатов. Сертифицированные детали гарантируют соответствие международным стандартам безопасности и надежности.
- Анализ отзывов и опыта других предприятий. Реальные кейсы помогут оценить возможные риски.
- Расчёт полной стоимости владения. Важно учитывать не только цену запчасти, но и её ресурс, надежность и возможные затраты на устранение последствий отказа.
- Создание запаса ключевых комплектующих. Наличие резервных запчастей позволит избежать простоев и срочного поиска альтернативных решений, которые могут оказаться менее качественными.
Итог: правильный выбор запчастей – залог бесперебойного производства и работы ГПУ
Этот случай наглядно демонстрирует, что экономия на комплектующих может привести к многократно возросшим затратам в будущем. Производственные предприятия должны тщательно подходить к выбору запчастей, учитывая не только цену, но и качество, ресурс и возможные последствия в случае отказа.
Помните: правильное решение сегодня – это гарантированная надежность завтра.
Если у вас есть вопросы или вам нужна помощь в организации технического обслуживания, обращайтесь к нам!